Authorities condemn changes to requirements for many delays and rising costs. The NASA manager dramatically changed plans for the gateway program in 2020, and decided to launch PPE and Halo on the same rocket, prompting major design changes.
NASA administrator Trump candidate Jared Isaacman refused to commit to the Gateway program during a confirmation hearing in the Senate Commerce Committee on April 9. Sen. Ted Cruz (Sen. R-Texas), the chairman of the committee, pushed Isaacman on the Lunar Gateway. Cruise is one of the largest backers in the Gateway Programme’s Congress, as it is managed by the Johnson Space Center in Texas. If that goes on, Gateway guarantees numerous jobs in NASA mission control in Houston throughout its 15 years of life.
“That’s the area where I would like to roll up my sleeves and get a better idea of what’s right if confirmed. ” Isaacman replied to Cruz. “What are the opportunities Gateways present to us? And I think Gateways are a component of many programs that are beyond budget and behind schedule, so where are some of the challenges?
The pressure shell of the Residential and Logistics Front Post Base (HALO) module, which arrived in Gilbert, Arizona last week, arrived for internal equipment last week.
Credit: NASA/Josh Valcarcel
Check in at the gateway
Nevertheless, the Gateway program reached a milestone a week before Isaacman’s confirmation hearing. The metal pressure shell of the halo module was shipped from an Italian factory to Arizona. The Halo module is only partially completed and does not have the other hardware needed to operate in life support systems or spaces.
Over the next few years, Northrop Grumman will equip these components in its habitat and connect them with Silicon Valley’s Maxor Technology with power and propulsion elements under construction. This stage of spacecraft assembly and pre-lake testing reveals issues that can often reduce costs and cause more delays.
ARS recently spoke with John Olansen, a biomechanical engineer and veteran space shuttle flight controller who manages the gateway program at the Johnson Space Center. The transcription of the conversation with Olansen is below. Lightly edited for clarity and brevity.
ARS: Hello Module arrived in Arizona from Italy. What’s next?
Olansen: This Halo module has put a great effort in terms of primary and secondary structure in Thales Alenia Space, Italy. It focused on getting the vehicle ready to ship to Arizona. Now in Arizona, Northrop can be installed at Gilbert’s facility, running the missions we want to do, keep our crew safe and equipped with all the systems we need to make possible the science we want. So, considering a standard spacecraft, there is all the command and control functions, avionics systems, computers, network management, everything you need to control your vehicle. There is a supply distribution function. Halo is attached to power and propulsion elements, providing the main distribution capabilities of the entire station. It’s all part of the Hello. There is a standard thermal system for active cooling. There is a vehicle environment control system that needs to be installed. [along with] Some of the other crew systems you can think of, including lighting, suppression, mobility AIDS, all different types of crew systems. And then, of course, all of our scientific aspects. So, internally, there are both payload lockers and external payload sites available to us, so there are very few different systems needed for a human evaluation spacecraft.
ARS: What are the latest status of power and propulsion elements?
Olansen: PPE is on a fairly good pace in assembly and integration activities. The central cylinder is integrated with the propulsion tank…these propulsion modules are in good condition. They are working on the avionics shelves associated with the spacecraft. So, using both vehicles, we are about to complete the assembly in the next year or so, so we can enter into testing the integrated spacecraft at that point.
ARS: What are the important paths to reach the launch pad?
Olansen: Assembly and integration activities are truly key to us. It’s about reaching a complete vehicle-level test. All the various activities we work on throughout the vehicle have made substantial progress. So it’s about bringing them all together and assemble and integrate them into the right sequence. So it’s about getting the point where the vehicle can be put together in the way it is needed, and actually power it and do all the necessary tests. Obviously, software is an important part of its development activities, and when it supplies power to the vehicle, it allows it to perform all the control tasks needed by those vehicles.
[There are] Some important works I mention along those lines. On the PPE side there is an electric propulsion system. The thrusters associated with that system are being delivered. They will undergo acceptance tests at the Glen Research Center [in Ohio] It is then integrated into Maxar’s spaceship. The work is ongoing, as we speak. With ESA, ESA offers Halo Lunar communications systems. It will be streamed later this year. It is installed in Halo as part of the integrated testing and checkout and starts in Halo. This provides the full communication capabilities to the moon, where PPE returns to Earth and provides communication capabilities. So these are important components we are considering delivering later this year.
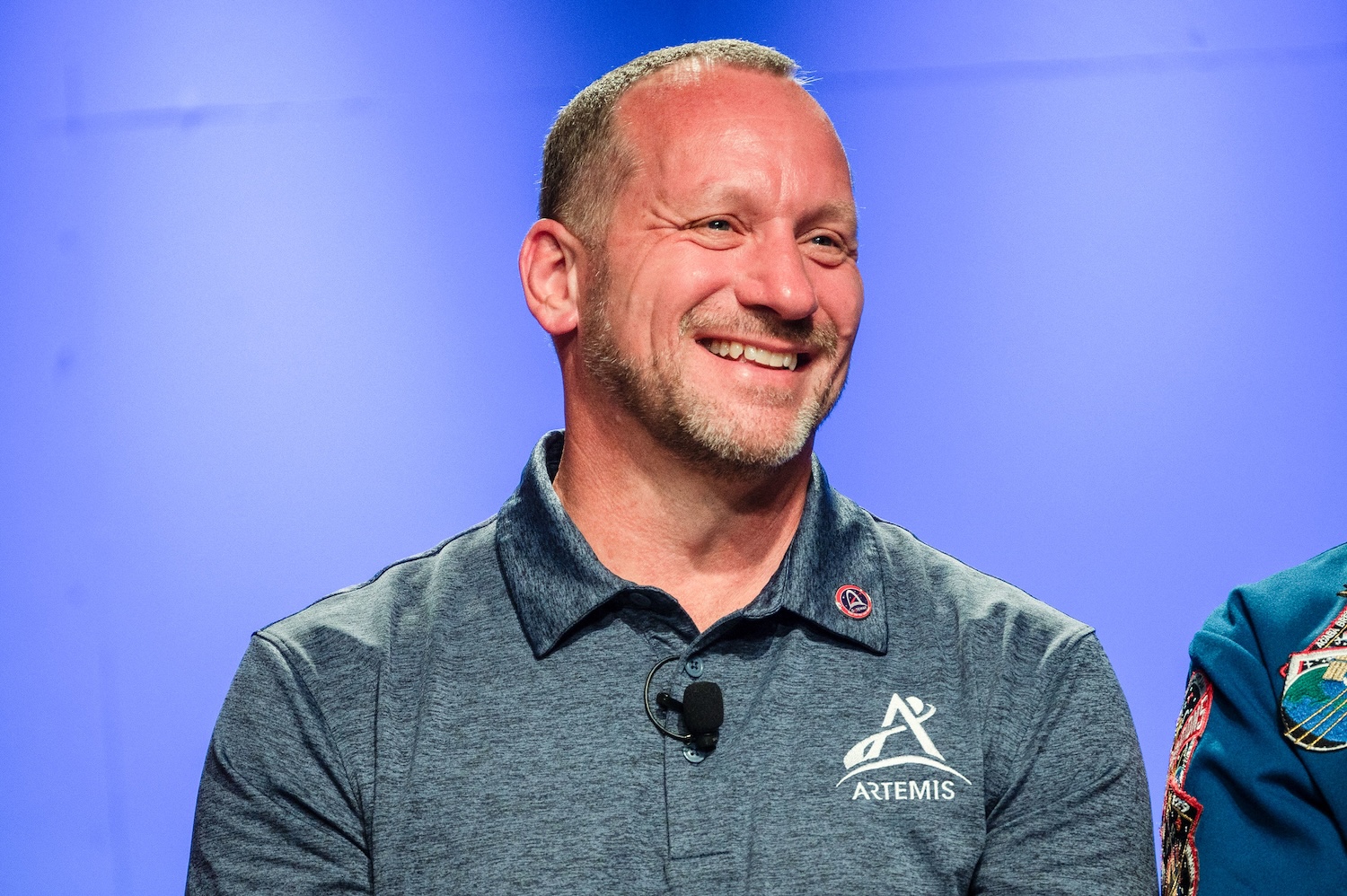
John Olansen, manager of NASA’s gateway program at Johnson Space Center in Houston.
Credit: NASA/Andrew Carlsen
ARS: What is the status of the PPE electric propulsion thruster?
Olansen: The first one is already actually delivered, so like I said, you will have the opportunity to go through acceptance tests for them. Other flight units are located just above the first flight units delivered. As I said, for integration into PPE, they do it through acceptance tests and then delivered to Maxar. So the work is already underway. [The Power and Propulsion Element will have three xenon-fueled 12-kilowatt Hall thrusters produced by Aerojet Rocketdyne, and four smaller 6-kilowatt thrusters.]
ARS: The Government’s Accountability Office (GAO) outlined concerns last year about maintaining a mass of gateways within the rocket’s capabilities. Has there been any progress on that issue? Should I remove components from the halo module and launch them in future missions? Do you narrow down the launch window and launch only on the most fuel-efficient orbit?
Olansen: We’re planning. We have released two vehicles together, so we are in the process of managing large quantities. It doesn’t make a difference for us, as mass management is always a matter of spacecraft development. Everything you described is all the knobs in the trading space as we progress, but basically we’re working on designing the best spacecraft that can be done first. So that’s the important part. When you deliver all of your components, you have several different options to measure mass on all of these components, understand what the integrated mass looks like, and allow you to perform missions that need to be performed. They all become balanced over time, based on the effects there. Many of these decisions need not happen today. I’ve already created what I need from a design perspective. What you need from making future decisions possible has already created them all. So, really, what we’re working on is that we can make the necessary decisions to fly the vehicle in the way we need it at the right time. [Near Rectilinear Halo Orbit, an elliptical orbit around the Moon]and then you can run Artemis missions in the future.
ARS: GAO also discussed the issues regarding Gateway controllability, which was as big as Starship docked. What is the latest status for that issue?
Olansen: As you can imagine, there are some risks that it can function as a program. We continue to look at all possibilities and work through them with due diligence. That’s our job and we can do it every day. It has stack controllability [issue]where it came for GAO, we were early in our assessment of what the potential impact is from visiting the vehicle. [vehicle] However, the vehicle visited. We are a smaller space station than the ISS. So it is to make sure you understand the meaning of thruster firing as the vehicle approaches the station, and the meaning associated with them is where that stack controllability conversation came from.
The buses that Maxar normally designed generally do not need to deal with docking. Part of what we are doing is working through ways that allow us to use different ways to provide the necessary control authority when visiting our visiting vehicles, and we can manipulate the visiting vehicles and their designs to ensure that we minimize impact on our stations. So the combination of these two has improved, primarily in terms of stack controllability, over the past year since the report was published. We are doing positive work to close all of the various potential cases there. We will continue to work through them. This is a standard forward task, but I was able to create some updates, some software updates, some administrative updates, and logic updates.